What Services We Offer?
We have precision CNC machining services that are the cornerstone of our manufacturing excellence.
CNC Machining Services
- Turning Process
- Milling Process
- Drilling Process
- Boring Process
- Tapping Process
- Grinding Process
- EDM Process
This process at Yueda Machining involves using computer-controlled lathes to rotate metal workpieces while cutting tools shape them into precise dimensions. This method ensures high accuracy and consistency, producing components with smooth finishes and tight tolerances. It is ideal for creating cylindrical parts such as shafts, bolts, and custom fittings.
- Material Types: Metals (e.g., aluminum, steel, brass), Plastics, and Composites.
- Turning Diameter: Typically ranges from 1 mm to 500 mm.
- Turning Length: Up to 2000 mm or more, depending on the machine.
- Tolerances: Can achieve tight tolerances, often within ±0.01 mm.
- Spindle Speed: Ranges from 100 to 6000 RPM.
- Surface Finish: Achievable surface roughness of Ra 0.8 µm or better.
- Tooling: Uses various cutting tools like carbide, high-speed steel (HSS), and ceramic inserts.
Our milling process involves using computer-controlled milling machines to remove material from a workpiece by rotating cutting tools. This method allows for precise shaping and detailing of complex parts with high accuracy. It is ideal for creating components with intricate geometries, such as gears, brackets, and custom-designed parts.
- Material Types: Metals (e.g., aluminum, steel, titanium), Plastics, and Composites.
- Milling Dimensions: Typically up to 1000 mm x 1000 mm x 500 mm.
- Tolerances: Can achieve tight tolerances, often within ±0.01 mm.
- Spindle Speed: Ranges from 1000 to 20000 RPM.
- Surface Finish: Achievable surface roughness of Ra 1.6 µm or better.
- Tooling: Uses various cutting tools like end mills, face mills, and ball nose cutters.
- Axes: Can operate on 3, 4, or 5 axes for complex geometries.
Our drilling process involves using computer-controlled drills to create precise holes in workpieces. This method ensures high accuracy and consistency, making it ideal for producing components with exact hole dimensions and placements. It is commonly used for creating holes for fasteners, threaded holes, and other detailed features in various materials.
- Material Types: Metals (e.g., aluminum, steel, titanium), Plastics, and Composites.
- Drilling Diameter: Typically ranges from 0.5 mm to 50 mm.
- Drilling Depth: Up to 10 times the diameter of the drill bit.
- Tolerances: Can achieve tight tolerances, often within ±0.05 mm.
- Spindle Speed: Ranges from 500 to 15000 RPM.
- Surface Finish: Achievable surface roughness of Ra 3.2 µm or better.
- Tooling: Uses various drill bits like twist drills, center drills, and step drills
Boring process at Yueda Machining involves enlarging existing holes in a workpiece using computer-controlled boring tools. This method ensures high precision and accuracy, making it ideal for achieving tight tolerances and smooth finishes in cylindrical holes. It is commonly used for refining and finishing holes to exact dimensions, ensuring they meet specific specifications for various industrial applications
- Material Types: Metals (e.g., aluminum, steel, titanium), Plastics, and Composites.
- Boring Diameter: Typically ranges from 1 mm to 500 mm.
- Boring Depth: Up to 10 times the diameter of the boring tool.
- Tolerances: Can achieve tight tolerances, often within ±0.01 mm.
- Spindle Speed: Ranges from 100 to 6000 RPM.
- Surface Finish: Achievable surface roughness of Ra 1.6 µm or better.
- Tooling: Uses various boring tools like single-point boring bars and boring heads
Tapping process at Yueda Machining involves using computer-controlled taps to create internal threads within holes. This method ensures high precision and consistency, making it ideal for producing threaded holes that meet exact specifications. It is commonly used for creating threads in various materials, allowing for secure fastening and assembly in mechanical components.
- Material Types: Metals (e.g., aluminum, steel, titanium), Plastics, and Composites.
- Tapping Diameter: Typically ranges from M1 (1 mm) to M36 (36 mm) threads.
- Tapping Depth: Up to 2.5 times the diameter of the tap.
- Tolerances: Can achieve tight tolerances, often within ±0.05 mm.
- Spindle Speed: Ranges from 100 to 3000 RPM.
- Surface Finish: Achievable surface roughness of Ra 3.2 µm or better.
- Tooling: Uses various taps like hand taps, spiral point taps, and forming taps
Grinding process at Yueda Machining involves using computer-controlled grinding machines to remove material from a workpiece, achieving a high-precision surface finish. This method is ideal for refining surfaces to tight tolerances and achieving smooth finishes on metal and other materials. It is commonly used for finishing parts that require high accuracy and surface quality, such as gears, bearings, and precision tools.
- Material Types: Metals (e.g., steel, aluminum, titanium), Ceramics, and Composites.
- Grinding Diameter: Typically ranges from 1 mm to 500 mm.
- Grinding Depth: Up to 0.5 mm per pass.
- Tolerances: Can achieve very tight tolerances, often within ±0.005 mm.
- Spindle Speed: Ranges from 1000 to 10000 RPM.
- Surface Finish: Achievable surface roughness of Ra 0.8 µm or better.
- Tooling: Uses various grinding wheels like aluminum oxide, silicon carbide, and diamond wheels
Electrical Discharge Machining (EDM) process at Yueda Machining uses electrical discharges to precisely remove material from a workpiece. This method is ideal for creating intricate shapes and fine details in hard materials that are difficult to machine with traditional methods. It is commonly used for producing molds, dies, and complex components with high precision and excellent surface finishes.
- Material Types: Hard metals (e.g., titanium, tungsten, hardened steels) and Conductive materials.
- Cutting Depth: Typically ranges from 0.1 mm to 500 mm.
- Tolerances: Can achieve very tight tolerances, often within ±0.005 mm.
- Surface Finish: Achievable surface roughness of Ra 0.2 µm or better.
- Electrode Materials: Commonly uses graphite, copper, and brass electrodes.
- Machining Speed: Varies based on material and electrode, but generally slower than conventional machining
Sheet Metal Fabrication
This process involves various techniques to shape and size metal sheets for manufacturing processes. Common methods include laser cutting, plasma cutting, and waterjet cutting, which ensure precision and efficiency. These processes are essential in producing high-quality components for various industries
- Material Types: Metals (e.g., aluminum, steel, stainless steel), and Alloys.
- Cutting Thickness: Typically ranges from 0.5 mm to 25 mm.
- Tolerances: Can achieve tight tolerances, often within ±0.1 mm.
- Cutting Methods: Laser cutting, plasma cutting, waterjet cutting, and mechanical cutting (e.g., shearing).
- Surface Finish: Depends on the cutting method, but laser cutting can achieve a smooth finish with minimal burrs.
- Cutting Speed: Varies based on material and thickness, with laser cutting being one of the fastest methods
Our bending process involves using a press brake to bend metal sheets into desired angles and shapes. This process is essential for creating parts with precise bends and tight tolerances, suitable for materials like aluminum, steel, and alloys. It ensures high accuracy and consistency, making it ideal for a wide range of industrial and commercial applications.
- Material Types: Metals (e.g., aluminum, steel, stainless steel), and Alloys.
- Bending Thickness: Typically ranges from 0.5 mm to 20 mm.
- Bending Radius: Generally, the minimum inside bend radius is equal to the material thickness.
- Tolerances: Can achieve tight tolerances, often within ±0.5 mm.
- Bending Methods: Press brake bending, roll bending, and air bending.
- Bending Angle: Can achieve angles from 0° to 180°.
- Tooling: Uses various dies like V-dies, U-dies, and custom dies
It is our process where a CNC machine uses a punch and die to create precise holes and shapes in metal sheets. This method is ideal for producing complex patterns and repetitive designs with high accuracy and efficiency. Suitable for materials like aluminum, steel, and alloys, it ensures tight tolerances and a clean finish, making it perfect for various industrial applications.
- Material Types: Metals (e.g., aluminum, steel, stainless steel), and Alloys.
- Punching Thickness: Typically ranges from 0.5 mm to 12 mm.
- Hole Size: Can create holes as small as 1 mm in diameter.
- Tolerances: Can achieve tight tolerances, often within ±0.1 mm.
- Punching Methods: CNC punching, turret punching, and single-station punching.
- Tooling: Uses various punches and dies, including round, square, and custom shapes.
- Punching Speed: Can perform up to 600 hits per minute, depending on the machine and material
This process involves joining metal sheets using advanced welding techniques such as MIG, TIG, and spot welding. These methods ensure precise and durable welds, suitable for various industrial applications. Our process guarantees high-quality results by adhering to strict material compatibility and technical specifications.
- MIG Welding: Ideal for thicker sheets, offering high-speed welding with minimal cleanup.
- TIG Welding: Provides precise and clean welds, perfect for thin sheets and intricate designs.
- Spot Welding: Suitable for joining overlapping metal sheets, commonly used in automotive and manufacturing industries.
- Aluminum: Requires specific settings to prevent oxidation and ensure strong welds.
- Stainless Steel: Needs controlled heat input to avoid warping and maintain strength.
- Carbon Steel: Versatile with various welding methods, providing robust and durable joints.
- Current and Voltage: Adjusted based on metal thickness and welding method.
- Welding Speed: Optimized to balance heat input and weld quality.
- Shielding Gas: Used in MIG and TIG welding to protect the weld pool from atmospheric contamination
The forming process is a manufacturing technique that involves the plastic deformation of materials, typically metals, to change their shape and size into the desired form and structure. This process utilizes various physical methods to manipulate the material, resulting in a product with specific geometrical characteristics.
- Bending: Using press brakes to bend metal sheets into specific angles and shapes.
- Stamping: Employing dies and presses to form complex shapes and patterns.
- Rolling: Passing sheets through rollers to create curved or cylindrical shapes.
- Aluminum: Requires careful handling to avoid cracking and maintain form integrity.
- Stainless Steel: Needs precise control to prevent deformation and ensure consistent shapes.
- Carbon Steel: Versatile for various forming methods, providing robust and durable components.
- Thickness Range: Depending on the forming method, can handle various sheet thicknesses.
- Tolerance Levels: Ensuring precise dimensions and consistency across formed parts.
- Forming Speed: Optimized to balance efficiency and quality of the formed components.
Surface Finishing
This process at Yueda Machining involves electrochemically treating aluminum to create a durable, corrosion-resistant oxide layer on the surface. This process enhances the material’s resistance to wear and can also be dyed in various colors for aesthetic purposes. It is ideal for applications requiring both functional and decorative finishes, providing long-lasting protection and improved appearance.
- Material Compatibility: Primarily used for aluminum and its alloys.
- Process Steps: Cleaning, pre-treatment, anodizing (electrolytic oxidation), coloring (optional), and sealing.
- Anodizing Types:
- Type I: Chromic acid anodizing.
- Type II: Sulfuric acid anodizing (most common).
- Type III: Hard anodizing (thicker and more durable).
- Thickness:
- Type II: Typically 5-25 microns.
- Type III: Typically 25-150 microns.
- Voltage: Varies depending on the type and desired thickness; generally between 15-100 volts.
- Temperature: Anodizing bath temperature ranges from 0°C to 20°C for hard anodizing and 20°C to 30°C for regular anodizing.
Surface finishing electroplating process at Yueda Machining involves coating a metal object with a thin layer of another metal through electrochemical deposition. This process enhances the object’s corrosion resistance, wear resistance, and aesthetic appeal. It is ideal for applications requiring a durable and attractive finish, providing long-lasting protection and improved appearance.
- Material Compatibility: Suitable for metals such as steel, copper, aluminum, and brass.
- Process Steps: Cleaning, surface activation, electroplating (using an electrolyte solution), rinsing, and drying.
- Plating Types:
- Nickel plating: Provides corrosion resistance and wear resistance.
- Chrome plating: Offers a hard, reflective surface.
- Gold plating: Used for conductivity and aesthetic purposes.
- Thickness: Typically ranges from 0.1 to 10 microns, depending on the application.
- Voltage: Varies depending on the type of metal being plated; generally between 2-12 volts.
- Temperature: Electrolyte bath temperature ranges from 20°C to 60°C.
This process at Yueda Machining involves meticulously smoothing and enhancing the surface of materials to achieve a high-gloss, reflective finish. This process includes multiple stages of abrasive polishing, from rough to fine, ensuring the removal of imperfections and achieving a flawless surface. It is ideal for applications requiring both aesthetic appeal and functional smoothness, providing a superior finish to meet high-quality standards.
- Material Compatibility: Suitable for metals, plastics, and other solid materials.
- Process Steps: Cleaning, rough polishing, intermediate polishing, and final polishing.
- Polishing Types:
- Mechanical polishing: Using abrasives and polishing wheels.
- Chemical polishing: Using chemical solutions to smooth the surface.
- Electrolytic polishing: Using an electrolytic solution to achieve a high-gloss finish.
- Abrasives: Various grits of sandpaper, polishing compounds, and diamond paste.
- Speed: Polishing wheel speeds typically range from 1,000 to 3,000 RPM, depending on the material and desired finish.
- Surface Finish: Achieves a smooth, reflective surface with a roughness average (Ra) as low as 0.025 microns.
At Yueda Machining, our surface finishing powder coating process provides a durable, high-quality finish for metal components. This process involves thorough surface preparation, electrostatic application of powder, and curing in a high-temperature oven. The result is a robust, corrosion-resistant, and aesthetically pleasing coating, ideal for enhancing both the appearance and longevity of your products.
- Material Compatibility: Suitable for metals like aluminum, steel, and iron.
- Process Steps: Surface preparation (cleaning and blasting), powder application (electrostatic spray), curing (heat treatment), and cooling.
- Types of Powder:
- Epoxy: Provides excellent adhesion and corrosion resistance.
- Polyester: Offers UV resistance and durability.
- Hybrid: Combines properties of epoxy and polyester.
- Thickness: Typically ranges from 50 to 150 microns, depending on the application.
- Curing Temperature: Generally between 160°C to 200°C for 10-20 minutes.
- Surface Finish: Available in various textures and gloss levels, from matte to high-gloss.
At Yueda Machining, our surface finishing painting process ensures a durable and attractive finish for various materials. The process includes meticulous surface preparation, primer application for enhanced adhesion, and precise paint application using advanced techniques. The result is a high-quality, corrosion-resistant, and aesthetically pleasing finish tailored to meet your specific requirements.
- Material Compatibility: Suitable for metals, plastics, and wood.
- Process Steps:
- Surface Preparation: Cleaning, degreasing, and sanding to ensure proper adhesion.
- Primer Application: Applying a primer coat to enhance paint adhesion and corrosion resistance.
- Paint Application: Using spray, brush, or dip techniques for even coverage.
- Curing: Air drying or oven baking depending on the paint type.
- Paint Types:
- Acrylic: Quick-drying, water-resistant, and UV-stable.
- Epoxy: High durability and chemical resistance.
- Polyurethane: Flexible and resistant to abrasion.
- Thickness: Typically ranges from 20 to 100 microns per coat.
- Curing Temperature: Varies with paint type; typically between 20°C to 150°C.
- Surface Finish: Available in various textures and gloss levels, from matte to high-gloss.
Prototyping
At Yueda Machining, our prototyping 3D printing process enables rapid and precise creation of prototypes. This process involves designing in CAD software, followed by layer-by-layer printing using advanced 3D printers. The result is a high-fidelity prototype that allows for quick testing and iteration, ensuring your final product meets all design and functionality requirements.
- Materials: PLA, ABS, PETG
- Printer Types:
- FDM (Fused Deposition Modeling): Suitable for most prototypes.
- SLA (Stereolithography): High-resolution and smooth finish.
- SLS (Selective Laser Sintering): Complex geometries and strong parts.
- Layer Resolution:
- FDM: 50-300 microns.
- SLA: 25-100 microns.
- SLS: 60-150 microns.
- Build Volume:
- Varies by printer model; typically ranges from 200x200x200 mm to 300x300x400 mm.
- Printing Speed:
- Depends on layer height and complexity; typically 40-100 mm/s.
- Post-Processing:
- Support Removal;
- Sanding and Polishing;
- Painting and Coating
At Yueda Machining, our prototyping CNC machining process delivers precision and efficiency. This process involves creating detailed CAD models, which are then converted into machine instructions. Using advanced CNC machines, we produce high-accuracy prototypes from various materials, ensuring they meet your exact design specifications and functional requirements.
- Materials: Metals, plastics, Composites
- Machine Types:
- 3-Axis CNC: Suitable for simple geometries.
- 5-Axis CNC: Ideal for complex shapes and undercuts.
- CNC Lathes: For cylindrical parts.
- Tolerances:
- Typically within ±0.005 mm to ±0.02 mm depending on material and part complexity.
- Surface Finish:
- Ra 0.8-1.6 µm: Standard machining finish.
- Ra 0.4 µm: Fine finish with additional polishing.
- Cutting Speed:
- Varies by material; typically 100-1000 mm/min.
- Spindle Speed:
- 5000-20000 RPM depending on material and tool.
- Tooling: End Mills, Drills, Taps
At Yueda Machining, our prototyping injection molding process is designed for efficiency and precision. This process involves creating a detailed CAD model, followed by the fabrication of a mold. Molten material is then injected into the mold to produce high-quality prototypes, allowing for thorough testing and validation before mass production.
- Materials:
- Thermoplastics: ABS, Polypropylene (PP), Polyethylene (PE);
- Thermosets: Epoxy, Silicone.
- Mold Types:
- Single-cavity molds: For low-volume production.
- Multi-cavity molds: For higher efficiency and volume.
- Family molds: Multiple parts in one mold.
- Cycle Time:
- Typically ranges from 30 seconds to 2 minutes depending on part complexity and material.
- Injection Pressure:
- Ranges from 50 to 200 MPa.
- Clamping Force:
- Typically between 20 to 2000 tons.
- Tolerances:
- Generally within ±0.1 mm.
- Surface Finish:
- SPI A-1 to D-3: Varies from high gloss to matte finish.
- Part Size:
- up to 500 x 500 mm.
At Yueda Machining, our prototyping laser cutting process ensures precision and efficiency. This process involves using high-powered lasers to cut and engrave materials based on detailed CAD designs. It allows for intricate patterns and shapes to be created quickly, making it ideal for producing accurate prototypes for testing and validation.
- Materials:
- Metals: Stainless Steel, Aluminum, Brass.
- Non-metals: Acrylic, Wood, Paper, Plastics.
- Laser Types:
- CO2 Lasers: Suitable for non-metals.
- Fiber Lasers: Ideal for metals.
- Nd:YAG Lasers: Used for high-precision cutting.
- Cutting Thickness:
- Metals: Up to 20 mm.
- Non-metals: Up to 50 mm.
- Cutting Speed:
- Varies by material; typically 1-20 m/min.
- Precision:
- Tolerances within ±0.1 mm.
- Power:
- CO2 Lasers: 30W to 200W.
- Fiber Lasers: 500W to 3kW.
- Beam Quality:
- M² < 1.2: Ensures high precision and quality.
- Surface Finish:
- Smooth edges with minimal burrs, often requiring no post-processing.
At Yueda Machining, our prototyping casting process is designed for precision and efficiency. This process involves creating a detailed mold from a master pattern, into which molten material is poured. Once the material cools and solidifies, it forms a high-quality prototype that can be used for testing and validation before proceeding to full-scale production.
- Materials:
- Metals: Aluminum, Zinc, Magnesium.
- Non-metals: Silicone, Polyurethane, Epoxy.
- Mold Types:
- Sand Casting: Suitable for larger parts.
- Investment Casting: High precision for complex shapes.
- Die Casting: High volume and detailed parts.
- Casting Tolerances:
- Generally within ±0.5 mm for metals.
- ±0.2 mm for non-metals.
- Surface Finish:
- Ra 1.6 to 6.3 µm: Varies based on the mold and material.
- Part Size:
- Can range from a few millimeters to several meters.
- Cooling Time:
- Varies by material and part size; typically minutes to hours.
- Post-Processing:
- May include machining, polishing, or heat treatment.
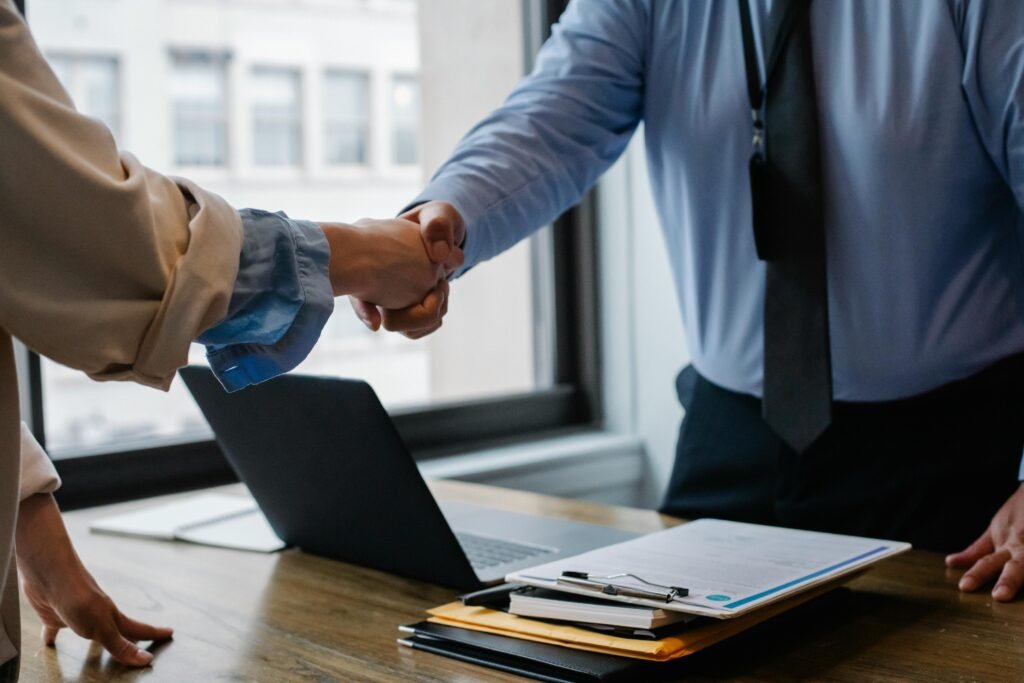
Let us together build a flourishing business
When connected with us, you aren’t growing your business alone. We have your back and put in our best to contribute to the growth of your entire team and organization. So, if you are looking for the right factory that’ll help you build a good foundation for your products, foster innovation, and streamline your supply chain, you’ve come to the right place.