Introduction of Smart Welding Robots
In the era of Industry 4.0 and smart manufacturing, Smart Welding Robots have emerged as the cornerstone of productivity in machining. According to the 2025 Laser Equipment Industry Analysis, the global welding robot market is projected to exceed $100 billion, with a CAGR of 6%-8% . These intelligent systems, integrating AI algorithms, 3D vision, and digital twin technology, are redefining traditional welding processes, driving transformations in automotive manufacturing, shipbuilding, aerospace, and other critical sectors.
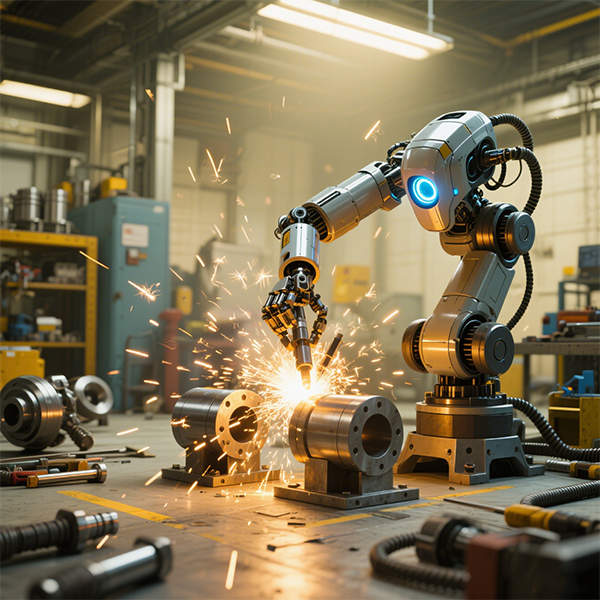
I. Intelligent Evolution of Mainstream Welding Processes
1. Precision Revolution in Arc Welding
Traditional manual arc welding relies heavily on welder expertise, with weld consistency errors up to ±0.5mm. In contrast, smart robots equipped with laser vision sensors dynamically adjust parameters (current, voltage) via real-time seam tracking, reducing errors to ±0.1mm . For instance, Bodor’s FSWELD2800 system achieves teachless welding for non-standard workpieces through parameter modeling and path optimization, boosting efficiency by over 30% .
2. Digital Transformation of Resistance Welding
Digital resistance welding leverages IoT platforms to monitor parameters and optimize processes via machine learning. Hunan Radiance’s smart spot welding system predicts weld quality through cloud data analysis, reducing false welding rates from 5% to 0.3% while cutting energy consumption by 20% . This breakthrough is particularly critical for precision welding in new energy vehicle battery modules, meeting lightweight and high-reliability requirements.
3. Cross-Disciplinary Integration in Laser Welding
Laser-arc hybrid welding excels in aerospace applications. CSSC Huangpu Wenchong’s intelligent welding system for large ship structures achieves deep penetration welding of titanium alloys through digital model-driven technology, extracting 1,000 weld paths in one operation and improving efficiency by 40% while enabling dynamic obstacle avoidance in confined spaces . This integration transforms laser welding from a single fusion method to a multi-dimensional manufacturing solution.
II. Core Value of Smart Welding Robots
1. Addressing Labor Shortages
China Welding Association reports a shortage of 400,000 senior welders by 2024, while each smart robot can replace 2.5 skilled workers . Hirebotics’ BotX Welder in the U.S., through its “robot-as-a-service” model, helped Wisconsin-based PMI LLC secure orders previously declined due to labor shortages, expanding its business by 20% . This model is rapidly spreading among SMEs.
2. Enhancing Quality & Efficiency
Deep learning-based systems detect and repair weld defects in real-time. Ruiji Technology’s 3D vision-guided system achieves a 98% first-pass weld quality rate via a “cloud-edge-device” architecture, eliminating post-weld grinding and reducing dust emissions by 60% . In shipbuilding, multi-robot collaborative welding shortens complex structure welding cycles by 35% with 70% less human intervention.
3. Enabling Green Manufacturing
Smart robots optimize parameters to reduce energy consumption, such as digital resistance welding systems improving energy efficiency by 30% . Welding fume purification and closed-loop recycling technologies lower workshop PM2.5 concentrations from 500μg/m³ to below 80μg/m³, meeting EU environmental standards.
III. Future Trends: From Automation to Autonomy
1. Full Autonomous Welding Breakthroughs
Reinforcement learning empowers robots to self-optimize. For example, simulating tens of thousands of welding processes enables robots to autonomously refine strategies for defect-free complex surface welding. Bodor’s digital twin system completes process simulation in virtual environments, reducing debugging time from weeks to days.
2. Cross-Platform Collaborative Ecosystems
5G and edge computing facilitate robotic clusters. CSSC’s intelligent welding system achieves multi-robot collaborative path planning and dynamic load balancing through cloud knowledge sharing, improving equipment utilization by 25% . This “cloud-edge-device” architecture is reshaping welding production.
3. Human-Robot Collaboration Paradigm
Force-controlled robots collaborate with welders, such as in nuclear power plant pipeline welding where robots handle high-temperature/radiation tasks while humans focus on intricate adjustments. This symbiosis ensures safety while preserving human creativity.
Conclusion
The rise of smart welding robots signifies a shift from “experience-driven” to “data-driven” machining. With deep integration of AI, IoT, and advanced manufacturing, welding evolves into a comprehensive solution integrating quality control, data analytics, and intelligent decision-making. For manufacturers, embracing this transformation is not just a competitive necessity but a gateway to global high-end manufacturing. As the 2025 Welding Market Outlook highlights, Asia will be the main fileld for smart welding, with China poised to lead through industrial chain advantages and policy support .